In 2016, Netflix debuted "Stranger Things," a sci-fi horror-thriller infused with 80s and 90s nostalgia. The show showcased menacing Demogorgon monsters with intricate flower-petal-like mouths. What might be surprising is that the designers opted for 3D printing technology to achieve the precise detail and texture needed, not with computer-generated imagery (CGI), as one might assume.
Welcome to the world of 3D printing, a cutting-edge technology that is reshaping many different industries and redefining manufacturing processes globally.
In this explainer, we dive deep into the world of 3D printing, exploring its revolutionary impact on healthcare, including complex medical devices.
What is 3D printing?

3D printing is a process of creating three-dimensional 3D products from a digital file.
The basic principle of 3D printing is to add material layer by layer to construct an object, which is a stark contrast to traditional manufacturing methods that often involve cutting away material from a larger block.
3D printing creates objects layer by layer from a digital design. A 3D printer melts or solidifies material like plastic or metal, depositing it one thin slice at a time to build up the final 3D shape. It's like making a sculpture from many stacked sheets of paper.
Difference between 3D printing and traditional manufacturing

Because the process starts with nothing and adds material, 3D printing is also called additive manufacturing. Conventional manufacturing processes, on the other hand, are called subtractive manufacturing (because they remove material)
Understanding the 3D printing process

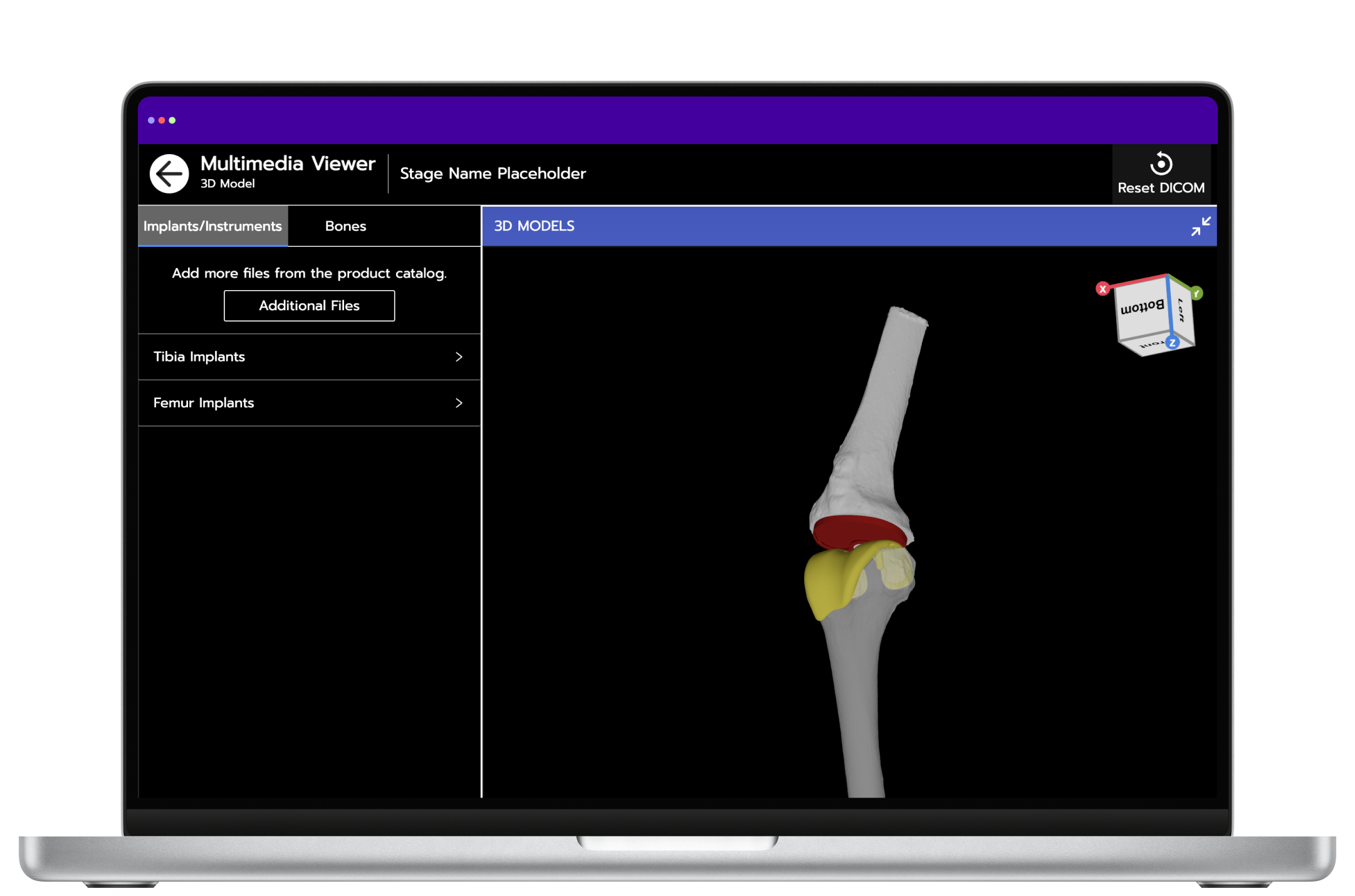
Step 1: 3D modeling and design
A 3D printed object’s journey starts with a concept translated into a digital format using 3D planning software. This software is crucial for detailed and precise models, serving as the blueprint for the final product.
The 3D modeling and design stage is a critical part of the 3D printing process, where ideas and concepts are transformed into digital models that can be printed.
The steps involved in 3D planning of 3D printed products are:
Conceptualization: The first step in the 3D printing process is conceptualizing the design. This involves identifying the purpose, functionality, and aesthetic of the intended 3D model.
Whether it's a component for machinery or a medical device, clear objectives need to be set upfront.
3D design using 3D planning software: After conceptualization, the design is brought to life using 3D modeling software.
This software can range from sophisticated 3D planning software that uses artificial intelligence (AI) to more basic 3D modeling tools suited for consumer-level projects. With any
software, the designer creates a virtual 3D representation of the object, ensuring all measurements and specifications are accurate.
Testing and Refinement: Once the initial model is designed, it's common to run simulations or tests within the software to check for structural integrity, functionality, and aesthetics.
This step might involve iterating the design several times and validating the design with select stakeholders. This stage may include feedback from key customers to achieve the desired outcome.
File preparation for 3D printing: After finalizing the design, the 3D model is exported as a file format compatible with 3D printers, typically STL (Stereolithography) or OBJ format.
This file type describes the surface geometry of the 3D model without detailing color, texture, or other attributes.
Slicing the model: Before printing, the 3D model file needs to be 'sliced.' This is done using slicing software, which converts the model into a series of thin layers and produces instructions designed for a specific type of 3D printer.
This slicing process dictates how the printer will construct each layer based on the design.
Print preview and adjustments: Many slicing software applications offer a preview of how the printer will build the layers. This step is crucial for making final adjustments to print speed, resolution, and support structures required for overhangs or complex geometries.
Ready to print: With the sliced file ready, it’s transferred to the 3D printer electronically. The printer then reads the code and begins the printing process layer by layer.
Throughout this process, the key lies in marrying technical skill with creativity, ensuring that the final product is both functional and aesthetically pleasing.
The designer must consider the limitations and capabilities of the 3D printer and material to be used, as these factors significantly influence the design and final outcome.
Enhatch’s 3D planning portal offers one stop for you and your teams to plan all patient-specific surgeries from anywhere in the world.
Get in touchStep 2: Choosing the right material
Selecting the appropriate material for the final 3D printed product is a pivotal step in additive manufacturing. From plastics to metals, the choice depends on the object's intended function and required properties.
In healthcare, these materials must be biocompatible and withstand the pressures and stresses of our bodies’ movements and the effects of aging.
Step 3: 3D printing methods
Common additive manufacturing methods include:
- Fused Deposition Modeling (FDM)
- Stereolithography (SLA)
- Selective Laser Sintering (SLS)
Each technique has its advantages and limitations, impacting the object's strength, resolution, and appearance.
Step 4: Post-processing and inspection
After printing, objects often require cleaning, polishing, and finishing to enhance aesthetics and durability, ensuring they meet the set specifications.
Particularly in the healthcare industry, the products must meet stringent quality standards before being packaged and shipped.
Benefits of 3D printing in medicine

Here are some of the key ways in which 3D printing is influencing the field of medicine:
Customization and personalization
The most significant impact of 3D printing in medical devices is its ability to create personalized solutions like implants and surgical instruments.
Traditional implants are offered in standard sizes and shapes, which may not fit all patients perfectly. 3D printed implants can be designed and manufactured to match the specific anatomy of an individual patient.
Based on the design and manufacturing, this custom fit has the potential to improve the effectiveness of the implant and improve the quality of a patient’s life.
Complex geometries and design freedom
With 3D printing, designers can fabricate the most intricate of structures without worrying about the limitations of conventional manufacturing. As we know, the human body is complex; no two people are exactly alike.
Creative freedom in designing implants, organs, and other 3D products can help promote better health, faster recovery from surgery, and hopefully, an improved quality of life for millions.
Rapid prototyping and time to market
The speed of 3D printing is another significant advantage. Because design prototypes can be printed fast and relatively cost-effectively, medical device manufacturers and bioprinting companies can create designs, test, and iterate concepts, and develop game-changing products faster than before.
Biocompatible materials
3D printing technologies have advanced to use a variety of biocompatible materials, including metals, polymers, and ceramics. This enables a broad spectrum of uses, spanning from bone implants to providing support for soft tissues.
Innovative solutions for complex medical challenges
The flexibility of 3D printing has led to innovative solutions for complex medical problems. For example, implants can be designed to replace bone lost to cancer or to fit unique anatomical anomalies.
Better medical education and training
3D printed models of patient-specific anatomy can be used for pre-surgical planning and education, helping surgeons to plan more effectively and train on realistic models.
This is particularly useful in medical school and before complex surgeries.
Research and Development
The ease of prototyping and testing with 3D printing accelerates research and development in medical devices, leading to rapid advancements and innovation.
Among the most promising frontiers in healthcare technology is bioprinting. Bioprinting is a specialized application of 3D printing that uses living cells and biomaterials to create tissue-like structures. Bioprinting aims to address the critical shortage of transplantable organs. In the future, it can transform tissue engineering and regenerative medicine significantly. Bioprinting also has the potential to be used for testing drugs and understanding disease mechanisms. This technology is still in the experimental stage but has immense potential.
In summary, 3D printing in the realm of medical devices, particularly for personalized implants, offers numerous advantages, including customization, rapid production, cost-effectiveness, and the potential for innovative solutions to complex medical challenges. This technology is reshaping how medical treatments are approached, making them more efficient, effective, and tailored to individual patient needs.
Conclusion

3D printing is more than a technological advancement; it's a paradigm shift in how we create and think about creative solutions to complex problems, including in healthcare.
From additive manufacturing to the creation of life-changing medical devices, its implications are profound. As 3D planning software leverages the power of AI to offer greater precision, adaptability, and efficiency, the world of healthcare will become more personalized than ever before, with the goal of improving overall quality of life.